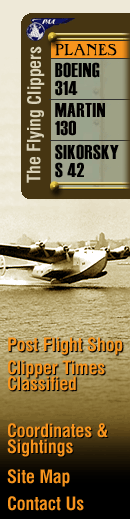
|
 |
|
 | |
 |
 |

 |  |
 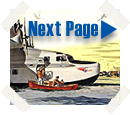 |
 |
 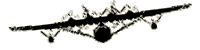
FEO Emil Kissel ret.1979
In Pan Am's training of graduate engineers to become flight engineers, we were assigned to all the various maintenance departments for practical experience and to make a formal report each time. The B314 toilets [3] dumped overboard through a fault prone system of levers, pumps etc. We had a test stand in our hangar at LaGuardia to overhaul them. The required hours spent to maintain them approached that required to maintain an engine. In my report, I suggested a redesign and was immediately assigned to do this. I managed to weasel out of this. All Flight Engineers knew the size of the box wrench to free it up during flight. The problem exists to this day. I once had a brand new 747 making its first revenue flight San Francisco to London. It had a full load of 400 passengers with 3 meals to be served. Over Reno, the purser informed me that NONE of the 12 toilets were flushing. We were able to solve the problem during flight. If you ask, I can give you the details. Our current airplanes still are subject to this problem.

The B314 had a streamlined navigators hatch located on the top surface of the wing mid chord. The seat located directly below was used by the navigator to take star shots to calculate their position. On the many test and training flights I made as an engineer, I used this seat when I had no other duties to watch our wake in the water during take offs. It was a thrilling site to see the changes in the water as the 4 powerful engines overcame the water drag and this large flying boat left the water. It was undoubtedly illegal.
Any waterborne aircraft has problems in a crosswind. The wind is trying to put the downwind wing into the water and if this happens to a B314 the outboard propeller hits the water and bends. Pan Am developed a system where it used the extra crew members to go out a ''catwalk" inside the wing to the outboard engine on the high wing to help move the wing to a horizontal position. This location was very noisy even at low power, but the engine on the high wing had to use lots of power to overcome the weather vane effect of the 3 fins. The sponsons on the 314 were not very effective and sailing knowledge was valuable in these conditions.

One of the tricky operations were at Horta, a harbor on the island of Fayal in the Azores. It is a small harbor surrounded by mountains. Landings could be made toward the mountains, but the longer takeoffs and small rate of climb meant takeoffs were made toward the open ocean. The design limited the waves to three feet in height because of the high stresses as the B314 hit the tops of the waves. The engineers job was to read the Captains accelerometer to warn him of the 8G? limit. During night takeoffs this was especially hard because we couldn't let our hooded flashlight spoil the darkened cockpit. This duty was normally performed by the second flight engineer kneeling between the pilots. There are photos of many B314s waiting in Horta harbor, for the waves to subside. I clearly remember the skill of our Horta employees in handling the thin skinned B314. They are a seafaring people.

Whenever a B314 over nighted anywhere, an anchor "watch" was used to save the airplane in case a strong wind came up and the anchor started dragging. At Shediac, New Brunswick, Canada a junior pilot and myself were assigned this duty, as there were not enough station personnel. So the two of us rowed out in rowboat and tied up to the B314. Soon it became cold and we had to rummage around to find some blankets because there was no source of heat. Then we became hungry and the nearest source of food was a lobster fish shop where we bought some lobster that had just been cooked. After rowing back to the B314 we found the shell to be so hard that we had to get the engineers tools to open them up. At dawn we rowed ashore thoroughly chilled to find out that the rest of the crew had attended the Saturday night dance in town. That was the first and last time that I volunteered to perform the anchor "watch."

The B314 wingspar was made from a round tube of aluminum that was rolled into an almost square shape. During this process, some undetected cracks occured. After the aircraft was built, they were detected, analyzed for strength and stop drilled to prevent propagation. There was also an ink line at each end of the crack to locate the drilled holes and to confirm that the crack did not propagate. During flight, flight engineers were required to inspect all of the B314 that was accessable, every 2 hours. This included these cracks. The wings were large enough to accommodate a crawl way out to #1 & #4 engines. We carried wrenches and a flashlight so we could repair any defects on the spot. As I remember it, one of the cracks was between the #3 and #4 engine. None of these cracks ever spread. At times we carried a spare engine and hoist in our cargo area so we would not be stranded with a failed engine in the boondocks. The whole crew was trained to do this engine change without help. Since the engine was larger than the hatch, the cylinders had to be installed after the crankcase was placed on top of the wing. I don't believe this was ever done. However, one of our intrepid engineers did change a defective magneto during flight using a good magneto from the spare engine. If he is still alive, he could give us the details of this extraordinary event. This "can do" attitude was typical of Pan Am in those days.

Aluminum and salt water corrode rapidly. Boeing's great engineering department minimized this by specifying Alclad - anodized, zinc chromated sheet aluminum. We had special brushes and chemicals to remove the white powdery corrosion and then we coated the wetted areas with lanolin. We all realized the life of the airplane would be short. The bilge, or the bottom deck was especially affected, because they were a series of water tight unventilated compartments. One had fuel transfer pumps.

The B314 departure from a small floating dock at Garden Bay Marine Terminal at LaGuardia Field, New York was complicated by the hazard of an fire during engine start with passengers aboard and only one exit door to walk out of. The 2 flight engineers are already aboard doing their check lists. The rest of the 12 crew members now formally marched aboard. There was a hawser from the bow to an underwater pulley and then ashore to a tractor. The tail had a special fitting that accommodated a quick release fitting that would be released by a beaching crew member who tied his rowboat to the same fitting awaiting the signal to release the taut stern line. After the 4 engines were started, the passengers walked aboard. The entry door was shut. The Captain signalled to be released. The tractor started pulling on the bow rope and when it was taut, the man in the rowboat released the tail rope and the B314 cleared the dock expeditiously. When the bow rope was loose the pilot threw the rope off the bow post, retracted them and closed the hatch. On one cold windy day, the man in the rowboat could not untie his rope and because the Captain did not know this, he started taxying out of Garden Bay in the usual crosswind. This was always tricky in this narrow bay. The alarmed man in the rowboat started beating on the fuselage above him. A passenger looking out saw this and informed the Purser who relayed this to the Captain on the deck above. They apparently solved the problem because there was never a report of a B314 arriving at Botwood, Newfoundland. Imagine the amazement there if this actually happened. This happened 60 years ago and this account is not history.

A significant part of Pan Am's reputation came from our Flight Service. I capitalize on purpose. On the B314 they often chose the food, cooked it, and served it in courses on linen tablecloths using specially designed silverware. We engineers were close to Flight Service because we fixed their galleys, controlled the temperature, fixed clogged toilets etc. They were males until the end of WW2. They were trained to help with engine changes. They were in charge of the ships papers and smoothed our entry through customs, immigration and public health in occasional unfriendly countries. Certain countries required bribes for short entry times, even today. Since they had many shore contacts, the pleasure of layovers in a man's city like Lisbon depended on how well you got along with the purser. They knew everybody.
During long flights when we were using low powers, it was necessary to speed up #3 engine because that's where the galley got its heat. During the engineers periodic inspections inside the wing, we paid special attention to leakage from the glycol lines that carried the heat to the galley from #3. They also conducted 'Clipper Dice'. There were 3 dice and six bets. Whenever pairs were rolled the odds favored the Purser and the passengers were HAPPY. Tips were normal in those days until the Captains found out that the Pursers were making more money than they were. No tipping continues since then. Whenever a B314 had an engine failure and had to come back with its untouched foods, everybody was devising ways to get to the food before the beaching crew. These guys were gorillas. I had to train with them and I remember a wintry day when we raided the galley for steak and ice cream and after we filled up, the gorillas allowed the rest in. This 'custom' continues to this day. After WW2, women were hired and this bachelor was in heaven. I would have paid them to fly. They didn't have to pay me. Our stewardesses came from every country in the world. There is a great story about our Nisei. I salute Pan Ams great Flight Service.
|
|  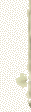  |
 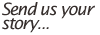 |
 |
|
 |
 |
|
 |
|


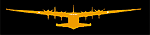
Copyright © 1999-2003 Flying Clippers All Rights Reserved All materials contained in http://www.flyingclippers.com are protected by copyright and trademark laws and may not be used for any purpose whatsoever other than private, non-commercial viewing purposes. Derivative works and other unauthorized copying or use of stills, video footage, text or graphics is expressly prohibited.
|
|